Los tiempos de inactividad no planeados en las empresas les cuestan millones de dólares cada año y las razones abarcan desde fallos en maquinaria, derrames accidentales, desastres naturales, bugs en el software, y muchas causas más. Además, este problema genera pérdidas en las instalaciones desde diferentes ángulos, como las pérdidas en ingreso, personal inactivo, costos de reparación, reajuste de inventario y reinicios en las lineas de producción.
Fundamentos del mantenimiento predictivo
En la actualidad, una de las formas de reducir los tiempos de inactividad es a través del mantenimiento predictivo. El mantenimiento predictivo consta de utilizar los datos operativos de una instalación para, a través de la detección de anomalías, encontrar indicios de posibles fallas que están por ocurrir en la maquinaria. Este mecanismo se perfila como la evolución natural del cuidado y preservación de maquinaria e infraestructura en el ámbito industrial dado el fuerte crecimiento en nuestra capacidad para procesar datos y realizar análisis sobre los mismos.
A diferencia del mantenimiento preventivo, que se programa en intervalos regulares sin considerar el estado actual de la maquinaria, el mantenimiento predictivo se basa en el seguimiento constante de las condiciones operativas del equipo para predecir cuándo se necesitará mantenimiento. Este enfoque permite realizar intervenciones precisas justo antes de que se produzcan averías, evitando así el coste y el tiempo perdido asociados a fallos inesperados.
Beneficios del mantenimiento predictivo:
- Reducción de costos operativos: Al evitar inactividad no planeada, se ahorra en costos de reparaciones de emergencia, los cuales suelen ser bastante elevados.
- Mejoras en la seguridad y confiabilidad: Prevenir fallos antes de que ocurran reduce el riesgo de accidentes e incrementa la confianza en la operatividad de la maquinaria.
- Optimizas la vida útil de tu equipo: El mantenimiento se realiza sólo cuando es necesario, evitando el desgaste adicional asociado a un mantenimiento excesivo o insuficiente.
- Eficiencia en la planificación de mantenimiento: Al predecir cuándo se necesitarán intervenciones, las empresas pueden organizar mejor sus recursos y personal.
Análisis de frecuencias: una herramienta clave
Pero, ¿cómo se recolectan y analizan los datos de la maquinaria? Uno de los métodos más efectivos es el realizar análisis sobre las vibraciones del equipo, tanto en desplazamiento, velocidad y aceleración a lo largo de sus tres ejes de movimiento. Para esto, se utiliza hardware especial, el cuál se instala en cada maquinaria y se encarga de recolectar la información. Este hardware, en casos complejos, puede estar fabricado de manera personalizada de acuerdo a las necesidades del corporativo o de las máquinas, mientras que otras veces, puede ser un dispositivo genérico que se puede adquirir a través de empresas como Treon o NCD.
Una vez recolectados los datos, se realizan análisis matemáticos tanto en los dominios de tiempo y frecuencia para encontrar anomalías en el comportamiento natural de la máquina y encontrar pequeñas fallas que puedan desencadenar en un tiempo de inactividad para la línea de producción. Esto es posible gracias a una amplia infraestructura digital que te permita recabar, almacenar, procesar y visualizar una cantidad masiva de datos de manera diaria y que utilice diferentes modelos de diagnóstico que ayuden a monitorear la salud de tus activos e identificar más de 40 fallas posibles para que puedas tomar acción y realizar un mantenimiento adecuado antes de que sea demasiado tarde.
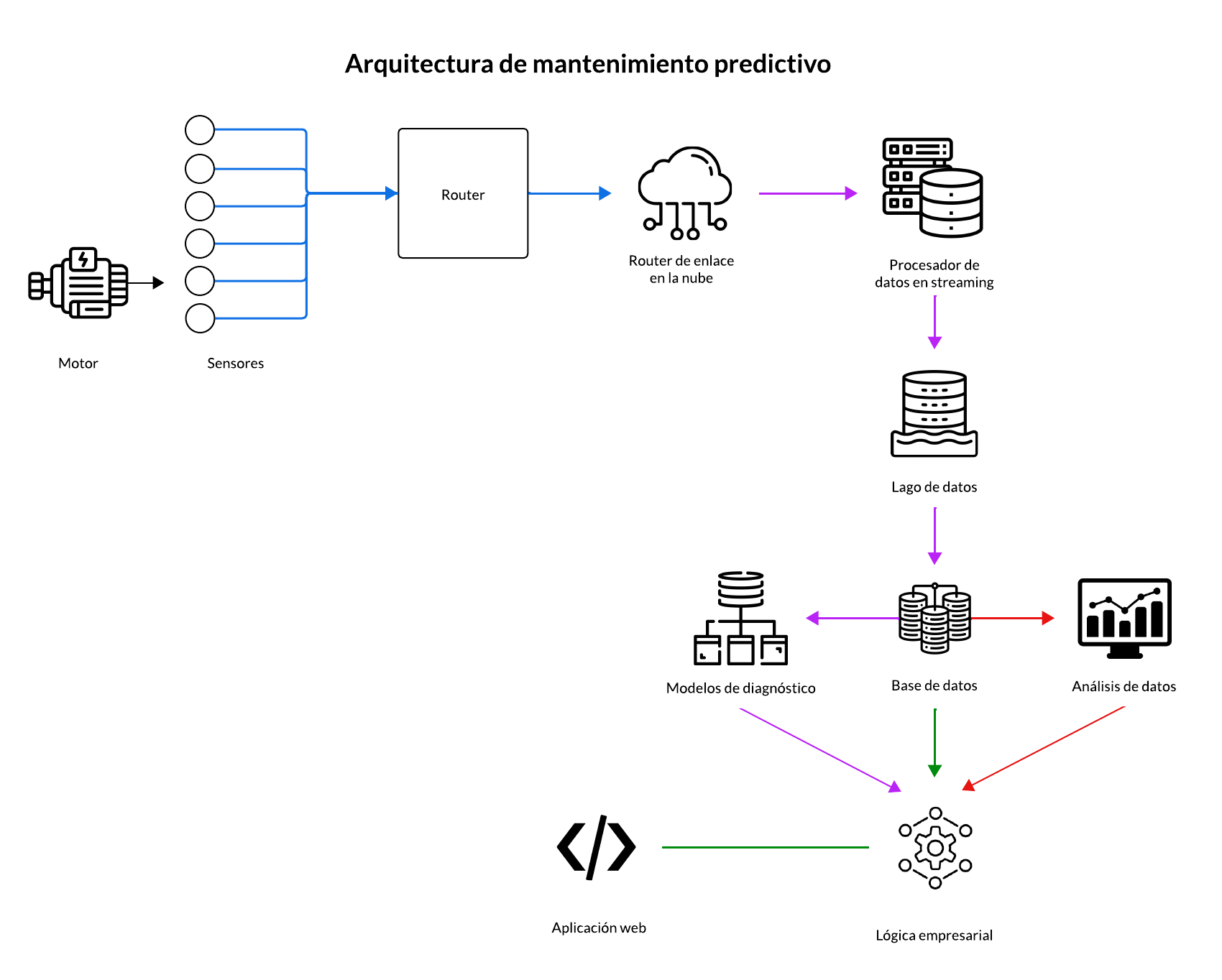
Las herramientas matemáticas que nos permiten visualizar y análizar el dominio de la frecuencia fueron algo que revolucionó radicalmente los panoramas de la ingeniería. Estos instrumentos matemáticos nos permite analizar la amplitud que tienen cada una de las frecuencias en una señal. Es decir, si tienes un motor operando a 100 revoluciones por segundo, lo más probable es que, a través de esta herramienta, notes una alta amplitud en la frecuencia de 100 hz. Esto es importante porque cada máquina, en cada condición diferente, dictamina valores diferentes en este dominio de frecuencia, y por ende, puedes encontrar fallos en tu maquinaria, a través de anomalías en este conjunto de valores.
Ventajas del análisis de vibraciones:
- Programación eficiente del mantenimiento: Al conocer el estado exacto del equipo, las empresas pueden planificar mejor las paradas de mantenimiento, minimizando el impacto en la producción.
- Detección temprana de fallos: Identifica anormalidades en las partes críticas de la maquinaria, como rodamientos, engranajes y ejes, antes de que resulten en fallos.
- Diagnóstico preciso: Ayuda a determinar la naturaleza y la severidad del problema, permitiendo una respuesta más efectiva y específica.
El análisis de vibraciones, por tanto, no solo actúa como un presagio que anuncia problemas futuros, sino como una brújula que guía hacia la acción preventiva más efectiva, asegurando que el mantenimiento predictivo cumpla su promesa de mantener la maquinaria en funcionamiento óptimo y los tiempos de inactividad al mínimo.
Implementación
Para implementar una solución de análisis de vibraciones en una empresa, existen principalmente tres vías: desarrollar la capacidad internamente, contratar un equipo de I+D externo para personalizar e implementar la solución, o adquirir y licenciar software existente de un proveedor confiable. Cada opción tiene sus ventajas y requisitos específicos.
Opción 1: Desarrollo Interno
La implementación interna implica evaluar las necesidades de la empresa, formar un equipo, adquirir el equipo de análisis de vibraciones, y desarrollar competencias internas para la operación y mantenimiento del sistema. Esta opción ofrece un mayor control sobre el proceso y la personalización de la solución, pero requiere una inversión significativa en tiempo, recursos y formación del personal.
Ventaja: La organización tiene total control de la implementación, personal y tiempo de desarrollo.
Desventaja: Requiere una inversión significativa en personal cualificado, tecnología y formación.
Opción 2: Contratación de un Equipo de I+D Externo
Una alternativa eficiente es subcontratar el proyecto a un equipo de I+D especializado. Esta opción permite a la empresa beneficiarse de la experiencia y el conocimiento técnico avanzado sin tener que preocuparse por los detalles de implementación. La empresa contratante puede especificar sus requisitos y expectativas, y el equipo externo se encargará de todo, desde el desarrollo hasta la puesta en marcha y el soporte post-implementación. Esta colaboración permite personalizar la solución para que se ajuste a las necesidades operativas y estratégicas de la empresa, desde la selección de sensores, hasta la integración con sistemas existentes y el análisis de datos.
Cómo funciona:
- Seleccionar un Proveedor: La empresa debe seleccionar un proveedor de servicios de I+D, la cual tiene una amplia experiencia en el desarrollo e implementación de este tipo de proyectos.
- Definición del Proyecto: Se define el alcance del proyecto, incluyendo objetivos, cronograma, y entregables esperados, en colaboración con el proveedor elegido.
- Acuerdo Financiero: La empresa y el proveedor acuerdan un modelo de financiación, que puede incluir pagos por etapas, una tarifa plana por el proyecto completo, o un modelo de pago basado en el éxito y los resultados obtenidos.
- Implementación, Adopción y Soporte: El equipo de I+D externo implementa la solución, realiza pruebas y ajustes necesarios, y proporciona formación y soporte al personal de la empresa.
Ventaja: El retorno sobre la inversión a menudo justifica este gasto debido a la reducción de tiempos de inactividad y el aumento de la eficiencia operativa.
Desventaja: Puede representar un costo inicial más significativo en comparación con soluciones internas básicas o licencias de software.
Opción 3: Adquisición de Licencia de Software Existente
La última opción es adquirir una licencia para un software de análisis de vibraciones ya desarrollado. Esta opción es la más rápida de implementar y requiere menos recursos internos, pero puede ofrecer menos flexibilidad en términos de personalización.
Cómo funciona:
- Evaluación de Software: La empresa evalúa diferentes soluciones de software disponibles en el mercado, teniendo en cuenta factores como la funcionalidad, facilidad de uso, compatibilidad con el hardware existente y costo.
- Compra y Licencia: Una vez seleccionado el software, la empresa adquiere las licencias necesarias y el proveedor del software ofrece formación y soporte técnico.
- Integración y Uso: El software se integra en los sistemas existentes de la empresa, y el personal recibe formación para comenzar a utilizar la herramienta en las operaciones diarias.
Ventaja: Es una forma muy rápida y sencilla de empezar a implementar el mantenimiento preventivo en la empresa y con un costo incial más bajo que las otras opciones.
Desventaja: El software licenciado puede no ofrecer todas las funcionalidades específicas que la empresa necesita o puede limitar la integración con otros sistemas.
Conclusión
En un mundo donde los tiempos de inactividad no planeados pueden significar millones de dólares en pérdidas para las empresas, la adopción de estrategias de mantenimiento predictivo y el análisis de vibraciones se presentan como soluciones cruciales. Estas técnicas no solo ayudan a evitar costosas interrupciones operativas sino que también mejoran la seguridad, la confiabilidad y la vida útil de la maquinaria. A través del uso de datos operativos y el análisis de frecuencias, las empresas pueden detectar anomalías y prevenir fallas antes de que estas ocurran, asegurando una programación eficiente del mantenimiento y la minimización del impacto en la producción.
Explorar la adopción de tecnologías de mantenimiento predictivo y análisis de vibraciones es un paso crucial hacia la optimización operativa. El objetivo es claro: minimizar los tiempos de inactividad y maximizar la productividad. Tomar la iniciativa hoy representa un mañana más productivo y rentable.